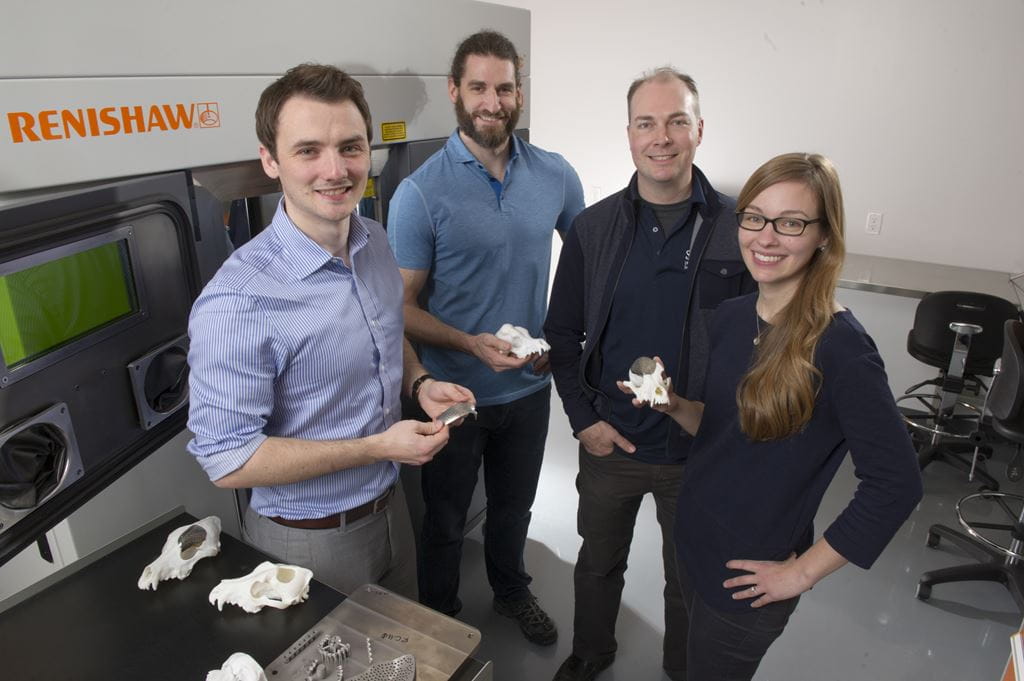
Made in CAMDT: Six projects that demonstrate innovative possibilities at Sheridan’s advanced manufacturing hub
Finding solutions to industry problems is at the core of the innovative work actioned by Sheridan faculty, students and staff at the Centre for Advanced Manufacturing and Design Technologies (CAMDT). Located at Davis Campus in Brampton, Ontario, the hub is one of six Research and Incubation Centres at Sheridan and houses industrial 3D printers, robotic arms, circuit board printers, laser and water-jet cutters and other advanced technologies. Students in related Faculty of Applied Science and Technology (FAST) programs have access to the equipment for experiential learning opportunities, which helps prepare them for the workforce.
Industry turns to CAMDT for access to its cutting-edge technology, the opportunity to work with a dedicated team of student researchers, and connection to staff and faculty experts. CAMDT-facilitated solutions have impacted many fields including healthcare, the arts, space, and the environment.
Below is a summary of six standout projects to emerge from CAMDT:
1. 3D medical model parts
A Sheridan team led by CAMDT Design Engineer and 3D Printing Medical Specialist, Dr. John Phillips, designed and produced full-colour and multi-material 3D medical model parts, with direct applications for the medical models industry. CAMDT’s “High Fidelity Medical Models” included 3D models ranging from organs to ultrasound phantoms, vessels and airways. The project was in collaboration with industry partner Candent Ltd., - a Mississauga-based source for human anatomical, dental models and nursing simulators. Funding was provided by the Southern Ontario Network for Advanced Manufacturing Innovation (SONAMI), of which Sheridan is a key partner.
2. Protective countertop shields for small businesses
Ramzy Ganady, Research Technologist at CAMDT, working on fabricating a protective countertop shield for an Ontario small business. Photo provided by Coca-Cola Canada.
In response to challenges small businesses are facing during the COVID-19 pandemic, CAMDT and Coca-Cola Canada partnered to design and fabricate protective countertop shields for distribution across Ontario. The shields, made of waterjet-cut plastic sheets and aluminum frames, were rapidly fabricated by an on-site team at CAMDT including Saleh Jiddawi, CAMDT Manager, and Ramzy Ganady, Research Technologist, in response to the phased re-opening of the economy to add a layer of protection when customers and staff are interacting. More than 200 will be distributed at no charge across Ontario and the designs will be made openly available so other businesses can benefit. Many of the shields make use of polyester PETG instead of plexiglass, which was in short supply during the pandemic.
Learn more about this community-focused partnership.
3. A new skull for Patches the dog
A nine-year-old dachshund from Pennsylvania named Patches had a brain tumour the size of an orange protruding from her forehead. Veterinary staff overseeing the surgery projected that removing it would leave a hole in 70 percent of her skull. In preparation for the surgery, Dr. John Phillips printed a 3D plastic model of Patches’ skull at CAMDT that allowed surgeons at Cornell University and the University of Guelph to prepare for the procedure – the first of its kind in North America. Dr. Phillips was also able to use Patches’ medical imaging data to design and 3D print a custom-fit titanium skull plate that was implanted after the tumour was removed.
Learn more about Patches the dog’s medical procedure via the Globe and Mail.
4. Additive manufactured experimental art
Film Path Camera Path with under-titles by Young and Giroux Projects Inc. Photo source: InterAccess Gallery
Alongside Canadian artists Daniel Young and Christian Giroux (Young and Giroux Projects Inc.) and with support from FedDev Ontario, principal investigator Dr. John Phillips utilized CAMDT's industrial 3D and metal printing equipment to bring their creative vision to life. The artistic duo set out to produce a large-scale, perceptual and conceptual puzzle for viewers that drew inspiration from a motion picture projector and film path. The use of various structural components for the sculpture were tested to evaluate multiple ways of creating the film looper structure and camera rigs with modern industrial solutions. In early 2019, the finished work titled Film Path / Camera Path with under-titles was featured at the InterAccess Gallery in Toronto.
5. Personalized devices to address pelvic floor disorders
Principal investigator Dr. John Phillips alongside industry partner COSM, a Toronto-based health-tech start-up, researched the feasibility of using 3D printing to produce custom medical-grade silicone models used to treat pelvic floor disorders. The use of pessaries – a prosthetic device inserted into the vagina to reduce the protrusion of pelvic structures – is a commonly prescribed first line of treatment for a pelvic floor condition called pelvic organ prolapse. Despite more than 10 million people using them globally, limitations and complications brought on by this treatment due to poorly-fitted devices is being explored by the CAMDT team using additive manufacturing. They’re working to create custom, patient-specific pessaries to improve the quality of life for people with pelvic prolapse.
6. Optimized wind turbines
The wind turbine created at CAMDT by a Sheridan team.
Dr. Joaquin Moran from FAST received an Ontario Centre of Excellence Voucher for Innovation Productivity (VIP)1 – NSERC Engage grant to assist in validating and optimizing the conceptual design for a patented Gyro-Cyclonic™ Generation wind turbine. Working with student researchers, in collaboration with Purus Power Corporation, the research included a Computational Fluid Dynamics (CFD) analysis to estimate the electrical power produced for different wind speed scenarios. Additionally, a physical prototype was fabricated based on optimization carried out on the computer model. Advanced manufacturing techniques at CAMDT were used in the fabrication, including waterjet cutting and 3D printing.
For industry interested in connecting with CAMDT, please email camdt@sheridancollege.ca.
Students who are interested in programs that have access to CAMDT should visit the Faculty of Applied Science and Technology pages.
Pictured at top of page: Dr. John Phillips, SONAMI Research Lead; Alex zue Linden, Ontario Veterinary College; Matt Parkes, ADEISS; Michelle Oblak, Ontario Veterinary College
Written by: Keiko Kataoka, Manager, Communications and Public Relations at Sheridan and Debbie Silva, Research Communications Officer in Sheridan's Research Office.
Media Contact
Meagan Kashty
Manager, Communications and Public Relations